Accounting
Purchase
Sales
Orders
Inventory
Returns
Sales Force Physical Returns
Schedule a Physical Return
Capture a Physical Return and Print a Returns Checking Slip
Validate a Physical Return
Create a Distributor Credit note
Sales Force Virtual Returns
Capture a Virtual Return and Print a Returns Checking Slip
Validate a Virtual Return
Issue a Distributor Credit note and Re-Invoice
Return to Supplier
Return to Supplier (Manual)
Internal Breakages
Distributor Breakages (Replacement)
Capture a Distributor Breakage (Replacements) and Print a Return Checking Slip
Validating a Distributor Breakage - Replacement
Distributor Breakages (Credit Note)
Capture a Distributor Breakage and Print a Returns Checking Slip
Validate a Distributor Breakage (Credit Note)
Create a Distributor Breakage Credit note
Adjustments
Corrections
Products
Manufacturing
Attendance Register
Help
Additional Help
Installing Odoo as an application
Two Factor Authentication Set Up
Automated Signature
How to Register a Guest on BBB - Guest Wi-Fi
Dot Matrix printing - How to and Troubleshooting
How to Log a Support Ticket in Odoo
How to Log a New Feature request Ticket in Odoo
Sales Force
Promotion
Demotion
Pay-In Sheets
Create and print pay-in sheets pack
Register pay-in sheets
Capturing pay-in sheets
Register pay-in sheets distributor summaries
Capturing Pay-In Sheets Distributor Summaries
Create a Cosultant
Activating inactive sales force member
VoIP
Blacklisting
Suspend
Moving Consultants
Sales Force Member Information Edits
PaySpace
Contact Centre
MVNO
How to purchse data, voice, SMS and check the balance on BBB Connect HelpDoc
How to port/transfer your current SIM card number to BBB Connect SIM card
How to Recharge BBB Connect SIM card
TaskFlow
How to set up sales force meetings campaign
Making Inbound and Outbound calls for contacts 'Potential Leads'
How to create a user
How to make a sales force meeting call
How to set up extensions
How to configure sales force meetings
How to set up dispositions
How to set up a recruiting campaign
How to set up call teams
How to call the Leads and Recruits
Campaign Planner
Table of Contents
- All Applications
- Purchase
- Orders
- Local Purchase Order
- Creating a Receipt
Creating a Receipt
Introduction
Once the stock has arrived at the warehouse, The warehouse team will fill out a Delivery Slip of the counted/ Received stock, which will be signed off by the Warehouse manager and then sent to the Procurement team where the received quantity will be captured onto Odoo.
Responsible Team
- Warehouse Manager
- Receiving Personnel
- Procurement & Stock Management Clerk
- Procurement Manager
Navigation
Navigate to your Odoo dashboard and click on this application: Purchase
Navigate as follows to get to the correct screen:
Orders/ Validate Receipts
In the search bar at the top, type in the code of the Purchase Order, you should now land on a screen that looks like this:
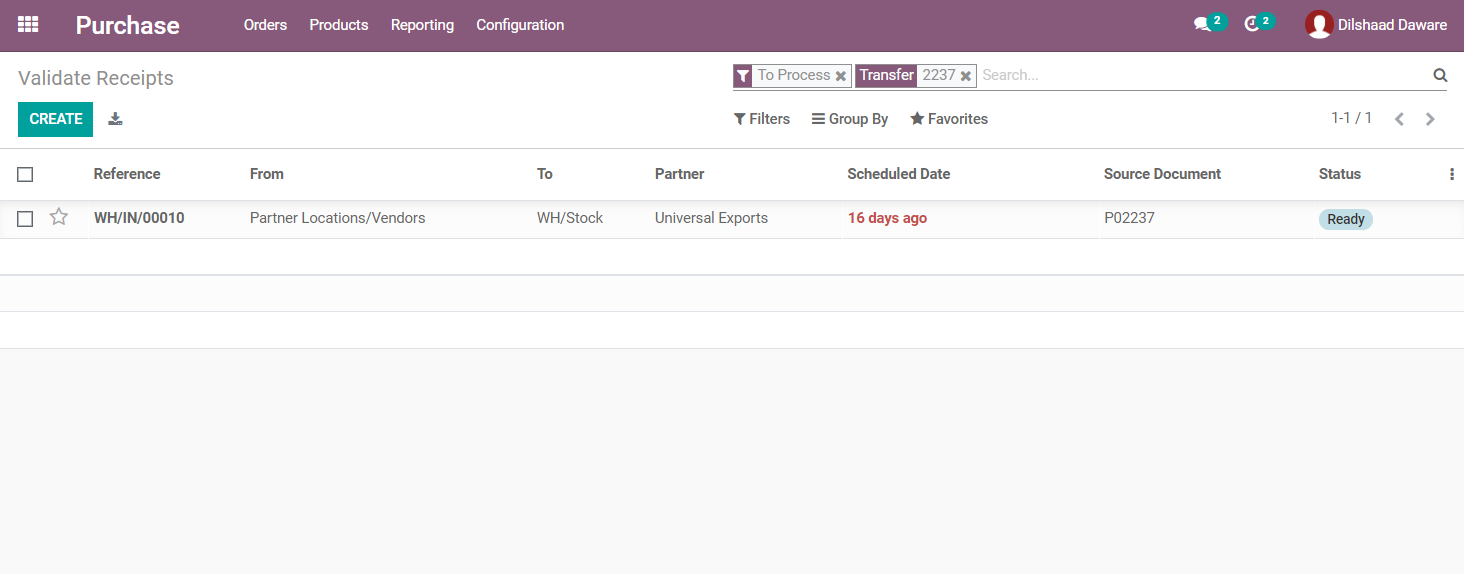
Process
- Select the Purchase Order and click [RECEIVE PRODUCTS].
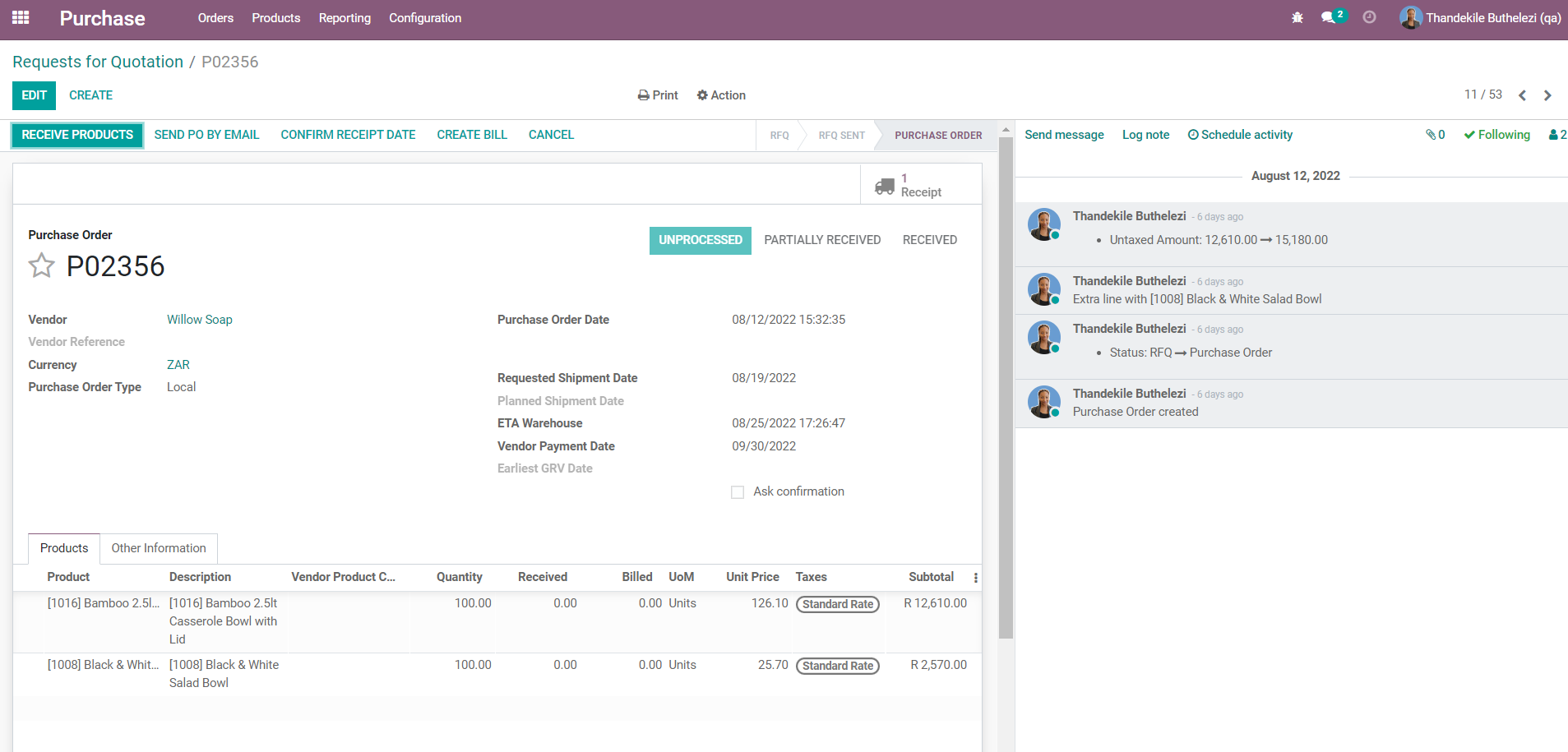
- Click [EDIT].
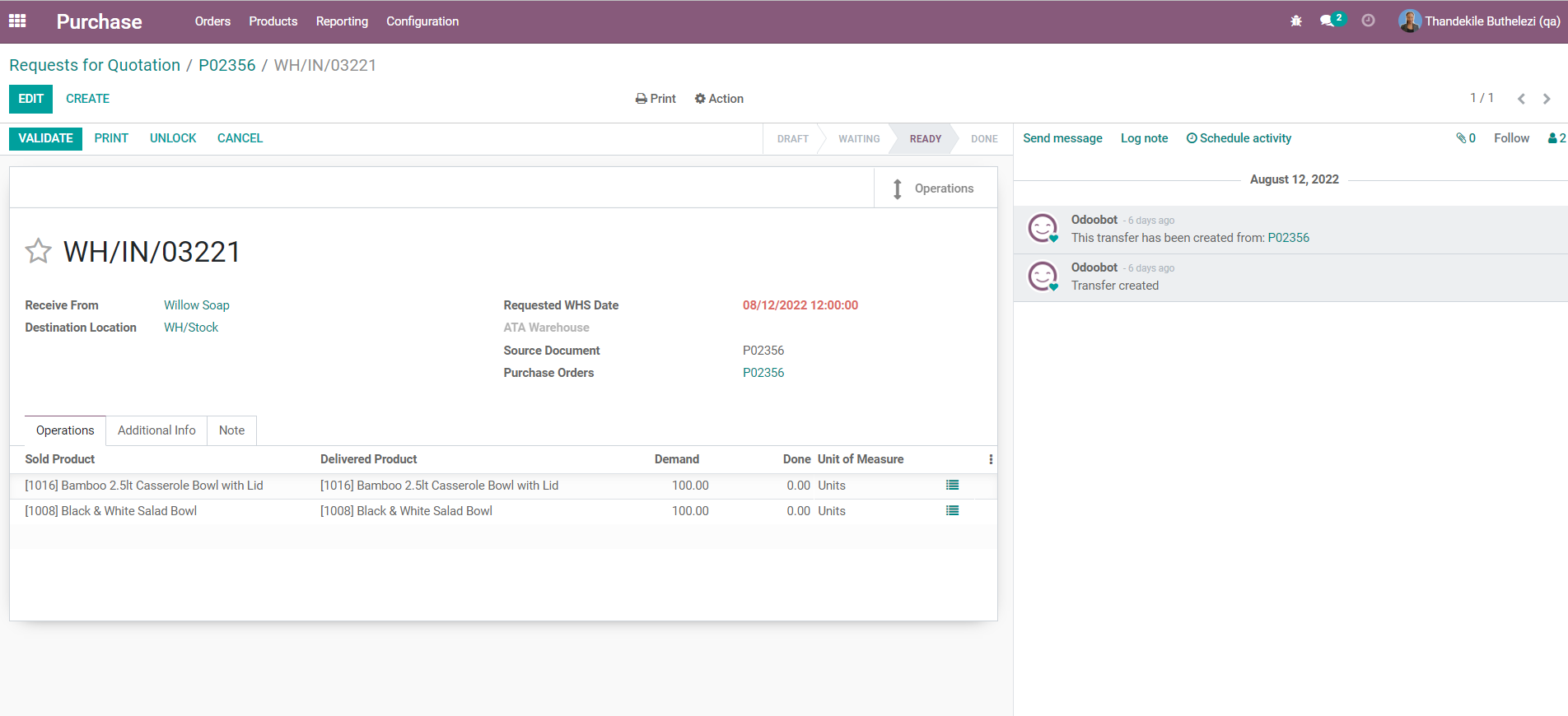
- Enter the Date of arrival under the field labelled 'ATA Warehouse'.
- Enter the received quantity under the input field Quantity according to the Blind Check Form count quantity.
- Click on [SAVE].
- Once all product quantities have been entered, click on [VALIDATE].
- The Quantity on hand values for these products have now been increased in WH/Stock on Odoo.
- When a user validates less stock than the ordered stock quantity, a backorder pop up screen appears asking the user to accept or decline the backorder. When the user accepts the Backorder, the following will happen:
- You will be required to enter a requested WHS date for the backorder, as shown on the screenshot below:
- Backorder Receipt will have a "Vendor Payment Date” field.
- The “Requested WHS Date” entered by the user will auto calculate the “Earliest Payment Date” using the vendor’s payment terms
- If a Receipt is not a Backorder, the “Earliest Payment date”, will be inherited from the PO Header with the same field name.
- You will be required to enter a requested WHS date for the backorder, as shown on the screenshot below:
- In an instance that the Vendor delivers a quantity lower or higher than the ordered quantity, do not change the ordered quantity to match the supplier's delivery
The weighted average cost per unit is calculated using the following formula:
When new Products arrive at the warehouse, the new average cost is computed as:
Average Cost = (Former Qty x Former Average Cost) +( Incoming Qty x Purchase+ Price) / Final Qty